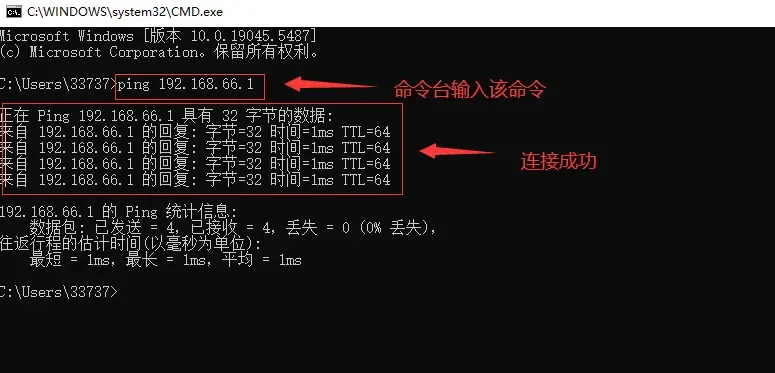
在当今竞争激烈的制造业环境中,预测性维护已成为提高设备可靠性和生产效率的关键策略。预测性维护通过对设备数据的实时监测和分析,能够在故障发生前预测潜在问题,从而减少停机时间和维护成本。以下是制造业预测性维护解决方案的实施路线图。
一、现状评估与目标设定
- 设备评估 :全面盘点企业现有设备,包括设备类型、品牌、型号、运行状况等详细信息。分析每台设备的历史故障数据和维护记录,确定关键设备和易出故障的部件。
- 需求分析 :与各部门(如生产、维护、管理层)进行深入沟通,了解他们对预测性维护的需求和期望。明确预测性维护的目标,如减少停机时间、降低维护成本、提高生产效率等。
- 制定目标 :根据评估结果和需求分析,设定具体的、可衡量的预测性维护目标。例如,在六个月内将关键设备的停机时间减少 20%,在一年内将维护成本降低 15%。
二、解决方案设计
- 技术选型 :选择适合企业需求的预测性维护技术,如振动分析、热成像、油液分析、声学监测等。评估不同的传感器、数据采集系统和分析软件,选择具有高精度、高可靠性和良好兼容性的产品。
- 架构设计 :设计预测性维护系统的整体架构,包括传感器网络、数据传输方式、数据存储和处理平台、用户界面等。确保系统具有可扩展性,能够适应企业未来的发展需求。
- 集成方案 :制定与其他生产系统(如 MES、ERP 等)的集成方案,实现数据共享和流程协同。确保预测性维护系统能够与现有系统无缝对接,提高整体运营效率。
三、数据采集与基础设施建设
- 传感器部署 :根据设备特点和监测需求,在关键设备上安装相应的传感器。确保传感器的安装位置正确,能够准确采集设备运行数据。
- 网络建设 :建立稳定可靠的网络基础设施,用于传感器数据的传输。可以选择有线网络、无线网络或混合网络,确保数据传输的实时性和安全性。
- 数据存储与管理 :搭建数据存储平台,选择合适的数据库和数据管理工具。确保数据的存储安全、可靠,并能够快速查询和分析。
四、模型训练与算法开发
- 数据预处理 :对采集到的数据进行清洗、过滤和归一化处理,去除噪声和异常值,提高数据质量。
- 特征提取 :分析设备数据,提取与设备故障相关的特征参数。例如,对于旋转设备,可以提取振动频率、振幅、温度等特征。
- 模型训练 :选择合适的机器学习算法或深度学习算法,如决策树、神经网络、支持向量机等,对历史数据进行训练,建立设备故障预测模型。
- 模型验证与优化 :使用验证数据集对训练好的模型进行验证,评估模型的准确性和可靠性。根据验证结果,对模型进行优化和调整,提高模型的预测性能。
五、试点运行与评估
- 选择试点设备 :在少量关键设备上进行预测性维护系统的试点运行,确保这些设备具有代表性,能够反映企业主要的生产过程和设备类型。
- 系统部署与测试 :在试点设备上部署预测性维护系统,进行功能测试和性能测试。确保系统的各项功能正常,数据采集准确,模型预测结果可靠。
- 效果评估 :收集试点运行期间的数据,评估预测性维护系统的实际效果。对比试点前后的设备停机时间、维护成本、生产效率等指标,分析系统的投资回报率。
- 问题分析与改进 :总结试点运行过程中遇到的问题和挑战,如数据采集不准确、模型预测误差较大、系统集成困难等。针对这些问题,制定相应的改进措施,为全面推广做准备。
、全面推广与持续改进
- 制定推广计划 :根据试点运行的结果,制定全面推广预测性维护系统的计划。确定推广的时间表、设备范围、资源需求等。
- 人员培训 :对维护人员、生产人员和管理人员进行预测性维护系统的培训,使他们熟悉系统的操作和使用方法,掌握数据分析和故障处理技能。
- 系统优化与升级 :随着企业生产规模的扩大和设备的更新换代,不断优化和升级预测性维护系统。更新传感器、数据采集系统和分析软件,提高系统的性能和功能。
- 持续改进 :建立持续改进机制,定期收集用户反馈和系统运行数据,分析系统存在的问题和不足。持续改进预测性维护策略和技术,适应企业不断变化的需求。
通过以上实施路线图,制造业企业可以成功地实施预测性维护解决方案,提高设备管理水平,降低运营成本,增强市场竞争力。在实施过程中,需要各部门的紧密合作和持续投入,确保预测性维护系统能够充分发挥其作用,为企业创造更大的价值。